디지털 트윈으로 미래 제조업 혁신하기: 2025년 최신 구현 가이드 🏭✨
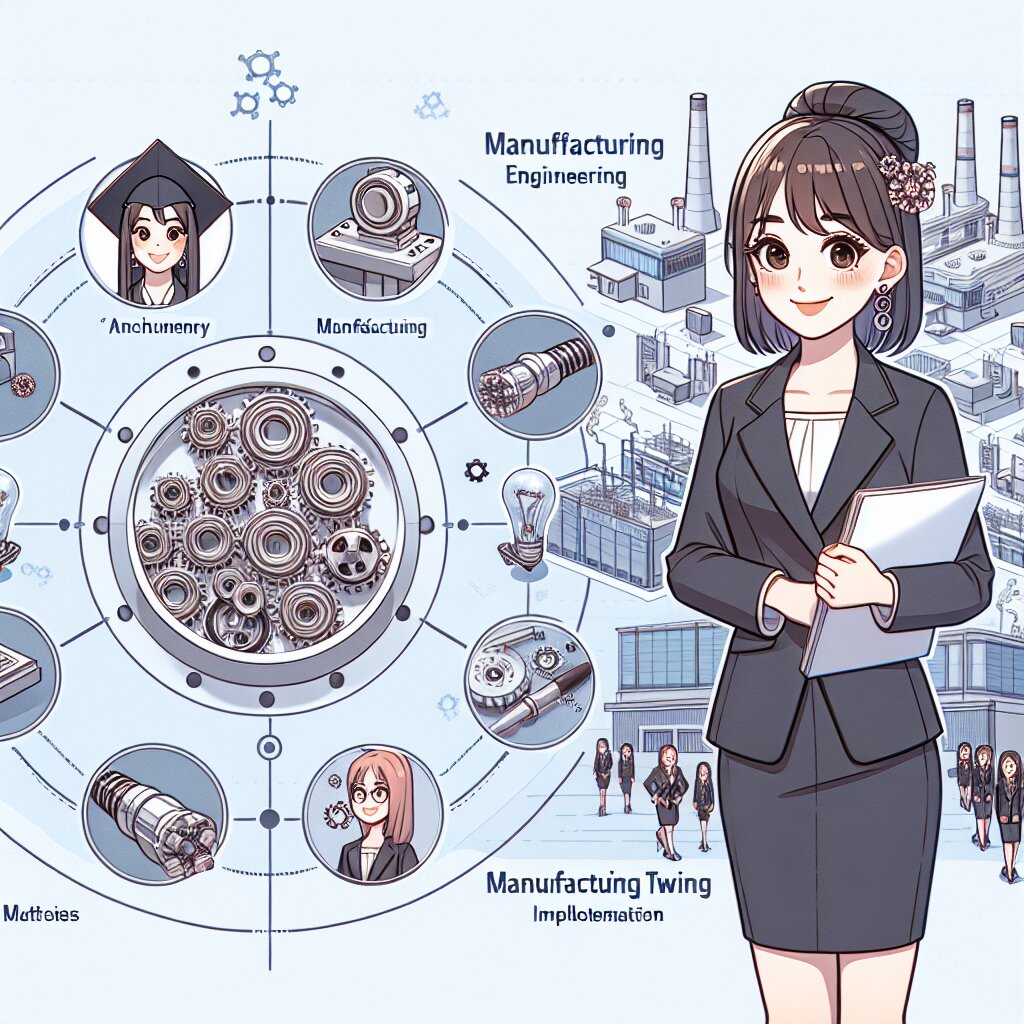
🌟 디지털 트윈이 뭐길래 다들 난리야? 🌟
2025년 현재, 제조업계에서 가장 핫한 키워드를 꼽으라면 단연 '디지털 트윈'이지! 근데 이게 정확히 뭐냐고? 간단히 말하면 현실 세계의 물리적 대상을 디지털 공간에 쌍둥이처럼 똑같이 복제해놓은 거야. 마치 네가 게임 속에 아바타를 만들어 놓은 것처럼, 공장이나 기계, 제품 같은 것들을 컴퓨터 속에 가상으로 만들어 놓는 거지.
근데 그냥 3D 모델링이랑은 달라! 디지털 트윈은 실시간으로 현실 세계의 데이터를 받아서 똑같이 움직이고, 심지어 미래도 예측할 수 있어. 예를 들어, 실제 공장에 있는 로봇이 움직이면 디지털 트윈 속 가상 로봇도 똑같이 움직이는 거야. 더 놀라운 건 이 가상 로봇으로 여러 시나리오를 테스트해보고, 그 결과를 실제 로봇에 적용할 수 있다는 거지! 😲
재능넷에서 최근 디지털 트윈 관련 프로젝트들이 급증하고 있다는 사실, 알고 있었어? 많은 제조업체들이 디지털 트윈 시스템 구축을 위해 전문가들의 재능을 찾고 있거든. 특히 시뮬레이션 전문가, 데이터 분석가, IoT 개발자들의 수요가 엄청나게 늘고 있어! 🔥
이 글에서는 2025년 최신 트렌드를 반영한 디지털 트윈 기반 제조 시스템을 어떻게 구현하는지 쉽고 재미있게 알아볼 거야. 기술적인 내용도 있지만, 너무 어렵게 생각하지 마! 마치 레고 블록 쌓듯이 하나씩 알아가다 보면 어느새 디지털 트윈 전문가가 될 수 있을 거야. 함께 미래 제조업의 핵심 기술을 탐험해보자! 👊
🤔 왜 갑자기 디지털 트윈이 중요해진 거야?
2025년 현재, 제조업은 그 어느 때보다 빠르게 변화하고 있어. 코로나19 이후 글로벌 공급망 재편, 지속가능성에 대한 요구, 맞춤형 생산 수요 증가... 이런 변화에 적응하려면 더 민첩하고, 더 스마트하고, 더 효율적인 제조 시스템이 필요해졌지!
🌈 디지털 트윈이 가져다주는 혜택들
- 실시간 모니터링과 예측 유지보수 - 기계가 고장 나기 전에 미리 알 수 있어! 🔍
- 가상 시뮬레이션으로 위험 감소 - 실제로 해보기 전에 컴퓨터로 테스트해볼 수 있어서 안전해! 🛡️
- 생산 최적화 - 어떻게 배치하고 운영하는 게 가장 효율적인지 알 수 있어! ⚡
- 에너지 절약 - 불필요한 에너지 소비를 줄여서 친환경적이고 비용도 절감! 🌱
- 제품 개발 시간 단축 - 시장에 더 빨리 제품을 내놓을 수 있어! 🚀
재미있는 사실! 2025년 초 발표된 글로벌 제조업 리포트에 따르면, 디지털 트윈을 도입한 제조 기업들은 평균적으로 생산성이 25% 향상되고, 유지보수 비용이 30% 감소했다고 해. 이런 숫자들이 바로 기업들이 디지털 트윈에 투자하는 이유지! 💰
특히 2024년부터 시작된 글로벌 탄소중립 규제 강화로 인해, 많은 제조업체들이 에너지 효율성을 높이기 위한 방법으로 디지털 트윈을 선택하고 있어. 실제로 한 자동차 부품 제조업체는 디지털 트윈을 통해 공장 에너지 사용량을 22% 줄이면서도 생산량은 15% 늘렸다고 하니, 정말 대단하지 않아? 🌍
이런 효과들 때문에 2025년 현재 전 세계 제조업체의 약 45%가 이미 디지털 트윈을 도입했거나 도입 중이라고 해. 특히 자동차, 항공우주, 전자제품 제조 분야에서 가장 활발하게 적용되고 있지. 그리고 이 추세는 앞으로 더 가속화될 전망이야! 🚀
🧩 디지털 트윈 시스템의 핵심 구성요소
디지털 트윈이 뭔지는 알겠는데, 이걸 어떻게 만드는 거야? 🤔 걱정마! 복잡해 보이지만 핵심 구성요소들을 하나씩 살펴보면 이해하기 쉬워. 마치 레고 블록처럼 이 요소들을 조합하면 디지털 트윈 시스템이 완성되는 거지!
1. IoT 센서와 액추에이터 🔌
디지털 트윈의 눈과 귀라고 할 수 있어! 실제 물리적 환경에서 온도, 습도, 진동, 압력 등 다양한 데이터를 수집하는 센서들이지. 2025년에는 초소형 나노 센서와 자가발전 센서가 대세인데, 배터리 교체 없이도 몇 년간 작동할 수 있어서 정말 편리해졌어.
최신 트렌드로는 엣지 컴퓨팅 기능이 내장된 스마트 센서가 인기야. 이 센서들은 데이터를 중앙 서버로 보내기 전에 자체적으로 일부 처리를 할 수 있어서 네트워크 부하를 줄이고 실시간성을 높여줘! 🚀
2. 데이터 통합 플랫폼 💾
다양한 소스에서 수집된 데이터를 한곳에 모으고 정리하는 플랫폼이야. 이게 없으면 데이터가 서로 다른 형식으로 흩어져 있어서 활용하기 어려워. 2025년에는 클라우드 기반 데이터 레이크와 하이브리드 아키텍처가 표준이 되었어. 특히 AWS IoT SiteWise, Azure Digital Twins, Google Cloud IoT 같은 서비스들이 많이 사용되고 있지.
재능넷에서도 이런 데이터 통합 플랫폼 구축 전문가들의 재능이 인기 있다고 해! 특히 다양한 산업 프로토콜(OPC UA, MQTT, Modbus 등)을 통합할 수 있는 전문가들이 귀한 존재지. 🌟
3. 3D 모델링 및 시각화 🖼️
디지털 트윈의 얼굴이라고 할 수 있어! 실제 물리적 대상을 컴퓨터 안에 3D로 표현하는 기술이지. 단순한 3D 모델을 넘어서 물리 엔진을 적용해 실제 물리 법칙을 따르는 시뮬레이션이 가능해. 2025년에는 AR/VR과 결합된 몰입형 디지털 트윈이 대세야.
최신 트렌드로는 Unity, Unreal Engine 같은 게임 엔진을 산업용으로 활용하는 사례가 늘고 있어. 이런 툴들은 원래 게임을 만들기 위한 거였지만, 뛰어난 그래픽 성능과 물리 시뮬레이션 능력 때문에 디지털 트윈 구현에도 많이 사용되고 있어! 🎮
4. AI/ML 분석 엔진 🧠
디지털 트윈의 두뇌라고 할 수 있어! 수집된 데이터를 분석해서 패턴을 찾고, 이상 징후를 감지하고, 미래를 예측하는 역할을 해. 2025년에는 강화학습과 연합학습 기술이 제조업 AI에 많이 적용되고 있어.
특히 주목할 만한 트렌드는 '설명 가능한 AI(XAI)'야. 이전의 블랙박스 같은 AI와 달리, 왜 그런 결정을 내렸는지 이유를 설명할 수 있는 AI가 산업 현장에서 중요해졌어. 사람들이 AI의 판단을 신뢰하고 따르기 위해서는 그 이유를 이해할 수 있어야 하거든! 🤖
5. 클라우드/엣지 컴퓨팅 인프라 ☁️
디지털 트윈 시스템의 근육이라고 할 수 있어! 모든 데이터를 처리하고 저장하는 컴퓨팅 파워를 제공해. 2025년에는 클라우드와 엣지의 하이브리드 모델이 표준이 되었어. 중요한 실시간 처리는 현장의 엣지 서버에서, 대규모 데이터 분석과 저장은 클라우드에서 이루어지는 방식이지.
최신 트렌드로는 '서버리스 컴퓨팅'과 '컨테이너 오케스트레이션'이 있어. 특히 Kubernetes를 활용한 마이크로서비스 아키텍처가 디지털 트윈 시스템에 많이 적용되고 있어. 이렇게 하면 시스템의 각 부분을 독립적으로 업데이트하고 확장할 수 있거든! 📦
6. 사이버 보안 시스템 🔒
디지털 트윈의 방패라고 할 수 있어! 중요한 산업 데이터와 제어 시스템을 해커로부터 보호하는 역할을 해. 2025년에는 제로 트러스트 보안 모델과 AI 기반 위협 탐지가 필수가 되었어.
특히 OT(운영 기술)와 IT(정보 기술)의 융합으로 인해 사이버 보안의 중요성이 더욱 커졌어. 해커가 디지털 트윈을 통해 실제 공장 설비를 제어할 수도 있기 때문에, 강력한 보안 시스템이 필수적이지! 🛡️
이 모든 구성요소들이 유기적으로 연결되어 작동할 때 진정한 디지털 트윈이 완성돼! 마치 인체의 각 기관처럼, 각 요소가 자기 역할을 제대로 수행해야 전체 시스템이 원활하게 작동하는 거지. 다음 섹션에서는 이런 디지털 트윈 시스템을 실제로 어떻게 구현하는지 단계별로 알아볼게! 🚀
🛠️ 디지털 트윈 기반 제조 시스템 구현 단계
자, 이제 디지털 트윈이 뭔지, 어떤 구성요소로 이루어져 있는지 알았으니 실제로 어떻게 만드는지 알아볼 차례야! 2025년 최신 방법론을 기반으로 한 단계별 구현 가이드를 준비했어. 너무 어렵게 생각하지 말고, 하나씩 따라와 봐! 🚶♂️
1단계: 목표 설정 및 범위 정의 🎯
디지털 트윈을 만들기 전에 먼저 "왜 만드는지", "무엇을 디지털화할지" 명확히 해야 해. 모든 것을 한번에 디지털 트윈으로 만들려고 하면 실패하기 쉬워. 작은 범위에서 시작해서 점진적으로 확장하는 게 2025년 현재 가장 성공률이 높은 접근법이야.
✅ 체크리스트:
- 어떤 비즈니스 문제를 해결하려는가? (예: 생산성 향상, 품질 개선, 에너지 절약)
- 어떤 자산이나 프로세스를 디지털화할 것인가? (예: 특정 생산라인, 개별 기계, 전체 공장)
- 어떤 데이터가 필요한가? (예: 온도, 압력, 진동, 에너지 사용량)
- ROI(투자수익률)는 어떻게 측정할 것인가?
- 주요 이해관계자는 누구인가? (경영진, 운영자, 유지보수팀 등)
2025년 트렌드: 최근에는 '밸류 스트림 매핑'이라는 방법을 많이 사용해. 전체 가치 흐름에서 가장 개선이 필요한 부분을 찾아내고, 그곳에 디지털 트윈을 우선 적용하는 거지. 이렇게 하면 투자 대비 효과를 빨리 볼 수 있어! 💸
2단계: 데이터 전략 수립 및 센서 인프라 구축 📊
디지털 트윈의 품질은 데이터의 품질에 직결돼. 어떤 데이터가 필요한지, 어떻게 수집할지, 얼마나 자주 수집할지 등을 결정해야 해. 그리고 필요한 센서와 데이터 수집 인프라를 구축하는 단계야.
🔍 주요 고려사항:
- 필요한 센서 유형 및 수량 (온도, 압력, 진동, 전력, 위치 등)
- 센서 정확도 및 샘플링 빈도 (초당 몇 번 데이터를 수집할지)
- 유선 vs. 무선 센서 네트워크 (2025년에는 5G/6G 기반 무선 센서가 대세)
- 데이터 전처리 전략 (엣지에서 얼마나 처리할지, 클라우드로 얼마나 보낼지)
- 기존 시스템(MES, ERP, SCADA 등)과의 통합 방안
실제 코드 예시: 2025년에는 Python과 Node-RED를 활용한 센서 데이터 수집이 일반적이야. 간단한 MQTT 기반 센서 데이터 수집 코드를 살펴볼까?
# Python으로 MQTT 센서 데이터 수집하기
import paho.mqtt.client as mqtt
import json
import time
from datetime import datetime
# MQTT 브로커 설정
broker_address = "mqtt.factory.local"
port = 1883
topic = "sensors/production_line_1/#"
# 콜백 함수 정의
def on_message(client, userdata, message):
try:
# 데이터 파싱
payload = json.loads(message.payload.decode("utf-8"))
sensor_id = payload["sensor_id"]
value = payload["value"]
timestamp = payload["timestamp"]
# 타임스탬프 변환
dt = datetime.fromtimestamp(timestamp)
formatted_time = dt.strftime("%Y-%m-%d %H:%M:%S")
# 데이터 처리 및 저장
print(f"센서 {sensor_id}에서 {formatted_time}에 {value} 값을 수신했습니다.")
# 여기에 데이터베이스 저장 로직 추가
except Exception as e:
print(f"데이터 처리 중 오류 발생: {e}")
# MQTT 클라이언트 설정
client = mqtt.Client("DigitalTwinDataCollector")
client.on_message = on_message
# 브로커 연결
client.connect(broker_address, port)
client.subscribe(topic)
# 메시지 수신 루프 시작
print("센서 데이터 수신 대기 중...")
client.loop_forever()
2025년 트렌드: 최근에는 '디지털 스레드(Digital Thread)'라는 개념이 중요해졌어. 이는 제품 수명 주기 전체에 걸쳐 데이터의 연속성을 유지하는 것을 의미해. 설계부터 생산, 운영, 유지보수까지 모든 데이터가 끊김 없이 연결되어야 진정한 디지털 트윈이 완성된다는 개념이지! 🧵
3단계: 3D 모델링 및 시각화 환경 구축 🖥️
이제 실제 물리적 대상을 디지털 공간에 표현할 차례야. CAD 모델을 기반으로 3D 디지털 트윈을 만들고, 실시간 데이터와 연동시키는 단계지. 2025년에는 게임 엔진 기반 시각화가 대세야!
🛠️ 주요 도구 및 기술:
- 3D 모델링 도구: AutoCAD, SolidWorks, Blender, Revit
- 게임 엔진: Unity Industrial, Unreal Engine 6.0, NVIDIA Omniverse
- 시각화 프레임워크: Three.js, Babylon.js, WebGL
- AR/VR 통합: Microsoft HoloLens 3, Meta Quest Pro 2, Apple Vision Pro
- 클라우드 렌더링: AWS Nimble Studio, Google Cloud Rendering
2025년 트렌드: 최근에는 '포토리얼리스틱 디지털 트윈'이 인기야. 단순한 3D 모델이 아니라 실제와 거의 구분이 안 될 정도로 사실적인 렌더링을 제공하는 거지. 특히 NVIDIA의 RTX 기술을 활용한 실시간 레이 트레이싱이 산업용 디지털 트윈에도 적용되고 있어! 🎨
4단계: 데이터 통합 및 분석 플랫폼 구축 🔄
이제 센서에서 수집한 데이터와 3D 모델을 연결하고, 분석 기능을 추가할 차례야. 실시간 데이터 처리, 저장, 분석을 위한 백엔드 시스템을 구축하는 단계지.
🧩 주요 구성요소:
- 데이터 통합 미들웨어: Apache Kafka, RabbitMQ, MQTT 브로커
- 시계열 데이터베이스: InfluxDB, TimescaleDB, Amazon Timestream
- 분석 엔진: Apache Spark, TensorFlow, PyTorch
- API 게이트웨이: Kong, AWS API Gateway, Azure API Management
- 대시보드 도구: Grafana, Power BI, Tableau
실제 코드 예시: 2025년에는 시계열 데이터베이스와 AI 모델을 연동하는 것이 일반적이야. 간단한 예측 유지보수 모델 코드를 살펴볼까?
# Python으로 예측 유지보수 모델 구현하기
import pandas as pd
import numpy as np
from sklearn.ensemble import IsolationForest
from influxdb_client import InfluxDBClient
# InfluxDB 연결 설정
url = "http://influxdb.factory.local:8086"
token = "your_influxdb_token"
org = "your_organization"
bucket = "machine_data"
# 데이터 가져오기
client = InfluxDBClient(url=url, token=token, org=org)
query_api = client.query_api()
query = f'''
from(bucket: "{bucket}")
|> range(start: -7d)
|> filter(fn: (r) => r["_measurement"] == "vibration_data")
|> filter(fn: (r) => r["machine_id"] == "pump_101")
|> aggregateWindow(every: 1h, fn: mean)
'''
result = query_api.query_data_frame(query)
# 이상 탐지 모델 학습
model = IsolationForest(contamination=0.05, random_state=42)
model.fit(result[['_value']])
# 새로운 데이터에 대한 이상 탐지
def detect_anomalies(new_data):
# 데이터 전처리
new_data = new_data.reshape(-1, 1)
# 이상 점수 계산 (-1에 가까울수록 이상치)
anomaly_scores = model.decision_function(new_data)
anomaly_labels = model.predict(new_data)
# 결과 반환
return {
"scores": anomaly_scores,
"is_anomaly": [1 if label == -1 else 0 for label in anomaly_labels]
}
# 실시간 모니터링 함수
def monitor_machine_health():
print("기계 상태 모니터링 중...")
# 여기에 실시간 데이터 스트리밍 및 분석 로직 추가
# 알림 설정
def send_alert(machine_id, anomaly_score):
print(f"⚠️ 경고: 기계 {machine_id}에서 이상 징후 감지! 점수: {anomaly_score:.2f}")
# 여기에 SMS, 이메일, 모바일 앱 알림 등의 코드 추가
2025년 트렌드: 최근에는 '디지털 트윈 오케스트레이션'이라는 개념이 등장했어. 여러 개의 디지털 트윈을 연결해서 전체 시스템을 통합적으로 관리하는 거지. 예를 들어, 개별 기계의 디지털 트윈들이 모여서 생산라인의 디지털 트윈을 구성하고, 여러 생산라인의 디지털 트윈이 모여서 공장 전체의 디지털 트윈을 구성하는 식이야! 🎼
5단계: 시뮬레이션 및 최적화 기능 개발 🔬
이제 디지털 트윈의 가장 강력한 기능인 시뮬레이션과 최적화 기능을 추가할 차례야. '만약 이렇게 하면 어떻게 될까?'라는 질문에 답할 수 있는 기능을 개발하는 단계지.
🚀 주요 시뮬레이션 유형:
- 이산 사건 시뮬레이션: 생산 라인의 병목 현상 분석
- 물리 기반 시뮬레이션: 기계 부품의 마모 및 고장 예측
- 몬테카를로 시뮬레이션: 다양한 변수에 따른 생산량 예측
- 디지털 쉐도잉: 실제 시스템과 디지털 트윈 간의 차이 분석
- 강화학습 기반 최적화: 최적의 생산 파라미터 도출
2025년 트렌드: 최근에는 '하이퍼 오토메이션'이라는 개념이 주목받고 있어. 디지털 트윈이 AI와 결합해서 자동으로 최적의 운영 조건을 찾고, 필요한 경우 실제 시스템에 적용까지 하는 거지. 사람의 개입 없이도 시스템이 스스로 최적화되는 단계로 발전하고 있어! 🤖
6단계: 사용자 인터페이스 및 대시보드 개발 👨💻
이제 사용자들이 디지털 트윈과 상호작용할 수 있는 인터페이스를 만들 차례야. 직관적이고 사용하기 쉬운 UI/UX를 개발하는 단계지. 2025년에는 AR/VR 기반 인터페이스가 대세야!
📱 주요 UI/UX 요소:
- 실시간 대시보드: KPI, 알림, 상태 모니터링
- 3D 인터랙티브 뷰: 확대/축소, 회전, 단면 보기
- AR 오버레이: 실제 기계 위에 데이터 표시
- VR 몰입 환경: 가상 공간에서의 협업 및 교육
- 음성 명령 인터페이스: 핸즈프리 조작
2025년 트렌드: 최근에는 '멀티모달 인터페이스'가 주목받고 있어. 터치, 음성, 제스처, 시선 추적 등 다양한 방식으로 디지털 트윈과 상호작용할 수 있는 거지. 특히 공장 현장에서는 양손이 자유롭지 않은 경우가 많아서, 음성 명령이나 AR 글래스를 통한 인터페이스가 인기를 끌고 있어! 👓
7단계: 테스트, 검증 및 배포 🧪
모든 시스템이 준비되었다면, 이제 테스트하고 검증한 후 실제 환경에 배포할 차례야. 디지털 트윈이 실제 물리적 대상과 정확히 일치하는지 확인하는 중요한 단계지.
✅ 검증 방법론:
- 디지털 쉐도잉: 실제 시스템과 디지털 트윈을 나란히 실행하며 비교
- 히스토리컬 데이터 테스트: 과거 데이터로 디지털 트윈의 정확도 검증
- A/B 테스팅: 디지털 트윈의 최적화 제안을 일부 영역에만 적용하여 효과 검증
- 스트레스 테스트: 극한 상황에서의 디지털 트윈 성능 검증
- 사용자 수용성 테스트: 실제 사용자들의 피드백 수집
2025년 트렌드: 최근에는 '지속적 검증(Continuous Validation)'이라는 개념이 중요해졌어. 한 번 검증하고 끝나는 게 아니라, 실제 시스템과 디지털 트윈 간의 차이를 지속적으로 모니터링하고 보정하는 거지. 이를 통해 시간이 지나도 디지털 트윈의 정확도를 유지할 수 있어! 🔄
8단계: 운영 및 지속적 개선 🔄
디지털 트윈은 한 번 만들고 끝나는 게 아니야. 지속적으로 데이터를 수집하고, 모델을 개선하고, 새로운 기능을 추가해야 해. 이것이 디지털 트윈의 진정한 가치를 실현하는 방법이지!
🔄 지속적 개선 전략:
- 모델 드리프트 모니터링: 디지털 트윈과 실제 시스템 간의 차이 추적
- 자동 모델 재학습: 새로운 데이터로 AI 모델 주기적 업데이트
- 피드백 루프 구축: 사용자 피드백을 시스템 개선에 반영
- 새로운 센서 및 데이터 소스 통합: 데이터 수집 범위 확장
- 디지털 트윈 확장: 더 많은 자산과 프로세스로 범위 확대
2025년 트렌드: 최근에는 '자기 진화형 디지털 트윈(Self-evolving Digital Twin)'이라는 개념이 등장했어. AI가 스스로 학습하면서 디지털 트윈 모델을 자동으로 개선하는 거지. 사람의 개입 없이도 시간이 지날수록 더 정확하고 유용해지는 디지털 트윈을 만드는 것이 목표야! 🌱
이렇게 8단계를 거치면 디지털 트윈 기반 제조 시스템이 완성돼! 물론 각 단계마다 세부적인 작업들이 많지만, 큰 그림으로는 이런 흐름을 따른다고 보면 돼. 다음 섹션에서는 실제 산업 현장에서 디지털 트윈이 어떻게 활용되고 있는지 사례를 통해 알아볼게! 🏭
📚 2025년 최신 디지털 트윈 성공 사례
이론은 충분히 알아봤으니, 이제 실제로 기업들이 디지털 트윈을 어떻게 활용하고 있는지 살펴볼까? 2025년 현재 가장 주목받는 디지털 트윈 성공 사례들을 소개할게! 이 사례들을 통해 디지털 트윈의 실질적인 가치와 적용 방법을 더 구체적으로 이해할 수 있을 거야. 🔍
🚗 테슬라의 기가팩토리 디지털 트윈
도전 과제: 테슬라는 2024년 출시한 새로운 배터리 생산 라인의 효율성을 극대화하고, 에너지 사용량을 줄이며, 불량률을 최소화해야 했어.
솔루션: 테슬라는 네바다 기가팩토리의 완벽한 디지털 트윈을 구축했어. 수천 개의 IoT 센서, 컴퓨터 비전 카메라, 로봇 데이터를 통합하고, NVIDIA Omniverse 플랫폼을 활용해 포토리얼리스틱 3D 모델을 만들었지. 특히 주목할 만한 점은 강화학습 기반 최적화 알고리즘을 적용해 생산 파라미터를 자동으로 조정한다는 거야.
결과: 디지털 트윈 도입 후 1년 만에 테슬라는 배터리 생산량을 32% 증가시켰고, 에너지 소비는 18% 감소시켰어. 또한 불량률이 45% 감소했고, 신제품 출시 시간이 30% 단축되었지. 테슬라의 CFO는 "디지털 트윈 프로젝트는 1년 만에 투자 비용을 회수했다"고 밝혔어.
핵심 기술: NVIDIA Omniverse, Azure Digital Twins, PyTorch 기반 강화학습, 5G 프라이빗 네트워크
🏭 지멘스의 스마트 팩토리 디지털 트윈
도전 과제: 지멘스는 독일 암베르크 공장에서 1,000개 이상의 제품 변형을 유연하게 생산하면서도 높은 품질과 효율성을 유지해야 했어.
솔루션: 지멘스는 자사의 MindSphere 플랫폼을 기반으로 전체 공장의 엔드투엔드 디지털 트윈을 구축했어. 이 디지털 트윈은 제품 설계, 생산 계획, 공정 시뮬레이션, 실시간 모니터링을 모두 통합했지. 특히 '디지털 스레드' 개념을 적용해 제품 수명 주기 전체에 걸쳐 데이터의 연속성을 유지했어.
결과: 디지털 트윈 덕분에 지멘스는 생산 라인 전환 시간을 60% 단축했고, 에너지 효율성은 25% 향상되었어. 또한 품질 문제를 실시간으로 감지하고 해결함으로써 불량률을 80% 감소시켰지. 가장 인상적인 것은 99.9996%의 품질 정확도를 달성했다는 점이야!
핵심 기술: Siemens MindSphere, Tecnomatix, NX CAD, TIA Portal, 에지 컴퓨팅
✈️ 에어버스의 항공기 디지털 트윈
도전 과제: 에어버스는 새로운 수소 추진 항공기 개발 과정에서 설계 최적화, 테스트 비용 절감, 인증 프로세스 가속화가 필요했어.
솔루션: 에어버스는 항공기의 전체 수명 주기를 아우르는 디지털 트윈을 개발했어. 설계 단계부터 운영, 유지보수까지 모든 데이터를 통합한 거지. 특히 CFD(전산유체역학) 시뮬레이션과 구조 분석을 실시간으로 수행할 수 있는 고성능 컴퓨팅 인프라를 구축했어.
결과: 디지털 트윈 덕분에 에어버스는 물리적 프로토타입 수를 75% 줄였고, 개발 시간을 2년 단축했어. 또한 시뮬레이션을 통해 발견된 설계 최적화로 연료 효율성이 15% 향상되었지. 가장 중요한 것은 안전 인증 과정이 크게 가속화되어 시장 출시 시간이 단축되었다는 점이야.
핵심 기술: Dassault Systèmes 3DEXPERIENCE, HPC 클라우드 컴퓨팅, 디지털 인증 프레임워크
🤖 삼성전자의 반도체 공장 디지털 트윈
도전 과제: 삼성전자는 최첨단 3나노 반도체 생산 과정에서 수율 향상, 에너지 효율화, 생산 일정 최적화가 필요했어.
솔루션: 삼성은 평택 반도체 공장의 멀티스케일 디지털 트윈을 구축했어. 개별 장비부터 전체 공정 라인, 그리고 공장 전체까지 다양한 스케일의 디지털 트윈을 계층적으로 연결한 거지. 특히 주목할 만한 점은 양자 컴퓨팅 알고리즘을 활용한 공정 최적화 시스템을 도입했다는 거야.
결과: 디지털 트윈 덕분에 삼성은 신규 공정의 수율을 초기부터 85%로 높일 수 있었고, 이는 기존 방식보다 30% 향상된 수치야. 또한 에너지 사용량이 22% 감소했고, 장비 가동률이 17% 증가했지. 가장 인상적인 것은 예측 유지보수 시스템을 통해 계획되지 않은 다운타임을 93% 감소시켰다는 점이야!
핵심 기술: 삼성 자체 개발 SDTP(Samsung Digital Twin Platform), AWS 양자 컴퓨팅, 6G 프라이빗 네트워크
이런 성공 사례들을 보면 디지털 트윈이 단순한 기술 트렌드가 아니라, 제조업의 미래를 근본적으로 바꾸는 혁신적인 접근법이라는 것을 알 수 있어. 각 기업들은 자신들의 특정 문제를 해결하기 위해 디지털 트윈을 맞춤형으로 구현했고, 그 결과 생산성, 품질, 효율성 측면에서 놀라운 성과를 거두었지! 🚀
재능넷에서도 이런 디지털 트윈 구현 프로젝트에 참여할 수 있는 다양한 전문가들을 만날 수 있어. 데이터 과학자, 3D 모델링 전문가, IoT 개발자, 클라우드 아키텍트 등 디지털 트윈 구현에 필요한 모든 인재들이 재능넷 플랫폼을 통해 협업하고 있지! 🤝
🧗♂️ 디지털 트윈 구현의 도전 과제와 해결책
디지털 트윈이 많은 혜택을 가져다주는 건 분명하지만, 구현 과정에서 여러 도전 과제에 직면하게 돼. 2025년 현재 기업들이 직면하는 주요 도전 과제와 그 해결책을 알아보자! 이런 문제들을 미리 알고 대비한다면, 디지털 트윈 프로젝트의 성공 확률을 크게 높일 수 있을 거야. 🛡️
1. 데이터 품질 및 통합 문제 📊
도전 과제: 디지털 트윈은 다양한 소스에서 수집된 데이터에 의존해. 하지만 서로 다른 형식, 주기, 정확도를 가진 데이터를 통합하는 것은 매우 어려운 일이야. 특히 레거시 장비에서 나오는 데이터와 최신 IoT 센서 데이터를 함께 활용해야 하는 경우가 많아.
해결책:
- 데이터 거버넌스 프레임워크 구축: 데이터 수집, 처리, 저장, 활용에 관한 명확한 정책과 절차를 수립해.
- ETL(Extract, Transform, Load) 파이프라인 구축: 다양한 소스의 데이터를 자동으로 수집하고 표준 형식으로 변환하는 파이프라인을 만들어.
- 데이터 품질 모니터링 시스템: 실시간으로 데이터 품질을 검증하고, 이상치나 누락된 데이터를 감지하는 시스템을 구축해.
- 데이터 메시(Data Mesh) 아키텍처: 2025년에 주목받는 접근법으로, 중앙집중식이 아닌 도메인 기반의 분산형 데이터 아키텍처를 구축해.
실제 사례: 한 자동차 부품 제조업체는 30년 된 장비와 최신 로봇이 혼재된 공장에서 디지털 트윈을 구축하려다 데이터 통합 문제에 직면했어. 이들은 레거시 장비에 에지 게이트웨이를 설치하고, 데이터 품질 점수 시스템을 도입해 문제를 해결했지. 그 결과 데이터 신뢰성이 95% 이상으로 향상되었어! 📈
2. 보안 및 개인정보 보호 문제 🔒
도전 과제: 디지털 트윈은 기업의 핵심 생산 데이터와 지적 재산을 디지털화하기 때문에 사이버 보안 위험이 크게 증가해. 특히 OT(운영 기술)와 IT(정보 기술)의 융합으로 인해 보안 취약점이 더 복잡해졌어.
해결책:
- 제로 트러스트 보안 모델 도입: "신뢰하지 말고 항상 검증하라"는 원칙에 따라, 모든 접근을 기본적으로 차단하고 필요한 경우에만 최소한의 권한을 부여해.
- 엔드투엔드 암호화: 데이터가 센서에서 수집되는 순간부터 저장, 처리, 시각화되는 모든 단계에서 암호화를 적용해.
- AI 기반 위협 탐지: 비정상적인 패턴이나 행동을 실시간으로 감지하고 대응하는 시스템을 구축해.
- 보안 중심 설계(Security by Design): 디지털 트윈 시스템을 설계할 때부터 보안을 핵심 요소로 고려해.
실제 사례: 한 에너지 기업은 디지털 트윈 구현 중 해킹 시도를 경험했어. 이후 그들은 OT/IT 네트워크 분리, 행동 기반 인증 시스템, 디지털 트윈 전용 보안 운영 센터(SOC)를 구축했어. 이러한 조치 덕분에 이후 1년간 보안 사고 없이 안전하게 운영할 수 있었지! 🛡️
3. 기술적 복잡성 및 인재 부족 👨💻
도전 과제: 디지털 트윈은 IoT, 클라우드, AI, 3D 모델링 등 다양한 기술의 통합이 필요한 복잡한 시스템이야. 하지만 이런 기술들을 모두 이해하고 통합할 수 있는 인재가 부족해. 2025년 현재 디지털 트윈 전문가는 가장 수요가 높은 IT 인력 중 하나야.
해결책:
- 모듈식 접근법 채택: 한 번에 모든 것을 구현하려 하지 말고, 작은 모듈부터 시작해 점진적으로 확장해.
- 내부 인재 육성: 기존 직원들에게 디지털 트윈 관련 교육과 훈련을 제공해. 특히 AR/VR을 활용한 몰입형 교육이 효과적이야.
- 외부 전문가 및 파트너십 활용: 컨설팅 기업, 기술 벤더, 학계와의 협력을 통해 전문 지식을 보완해.
- 로우코드/노코드 플랫폼 활용: 2025년에는 전문적인 코딩 지식 없이도 디지털 트윈의 일부 기능을 구현할 수 있는 플랫폼들이 많이 등장했어.
실제 사례: 한 중소 제조업체는 디지털 트윈 전문가를 고용하기 어려워 어려움을 겪었어. 그들은 재능넷 같은 플랫폼을 통해 필요한 전문가들과 프로젝트 기반으로 협업하고, 동시에 내부 직원들에게 체계적인 교육을 제공했어. 1년 후, 그들은 자체적으로 디지털 트윈을 운영하고 확장할 수 있는 역량을 갖추게 되었지! 🎓
4. ROI 증명 및 경영진 설득 💰
도전 과제: 디지털 트윈은 상당한 초기 투자가 필요한데, 그 효과가 즉시 나타나지 않는 경우가 많아. 경영진을 설득하고 지속적인 지원을 받기 위해서는 명확한 ROI를 증명해야 해.
해결책:
- 파일럿 프로젝트 시작: 전체 시스템이 아닌, 가장 효과가 클 것으로 예상되는 영역에 집중한 소규모 프로젝트로 시작해.
- 명확한 KPI 설정: 생산성, 품질, 에너지 효율성 등 측정 가능한 지표를 미리 정의하고 지속적으로 추적해.
- 단계적 가치 실현 계획: 단기, 중기, 장기적으로 어떤 가치를 창출할 수 있는지 로드맵을 제시해.
- 성공 사례 벤치마킹: 동종 업계의 성공 사례를 수집하고 분석해 참고 자료로 활용해.
실제 사례: 한 제약회사는 경영진을 설득하기 위해 생산라인 하나에 디지털 트윈 파일럿 프로젝트를 진행했어. 3개월 만에 생산 효율이 15% 향상되고, 품질 문제가 30% 감소하는 성과를 보여주었지. 이 결과를 바탕으로 전체 공장으로 확대하는 5년 계획에 대한 투자를 승인받을 수 있었어! 📊
5. 레거시 시스템 통합 문제 🔄
도전 과제: 대부분의 제조 기업들은 오래된 레거시 시스템과 장비를 보유하고 있어. 이런 레거시 시스템을 최신 디지털 트윈 아키텍처와 통합하는 것은 큰 도전이야.
해결책:
- 레거시 시스템 어댑터 개발: 오래된 시스템과 새로운 플랫폼 사이에 데이터를 변환하고 전달하는 중간 계층을 만들어.
- 에지 컴퓨팅 활용: 레거시 장비에 에지 디바이스를 연결해 데이터를 수집하고 전처리해.
- 점진적 현대화 전략: 한 번에 모든 것을 교체하지 말고, 단계적으로 레거시 시스템을 현대화해.
- 디지털 래퍼(Digital Wrapper) 접근법: 레거시 시스템을 그대로 두고, 그 위에 디지털 레이어를 씌우는 방식으로 접근해.
실제 사례: 한 철강 제조업체는 30년 된 설비와 최신 설비가 혼재된 환경에서 디지털 트윈을 구축하려 했어. 그들은 레거시 장비에 산업용 IoT 게이트웨이를 설치하고, OPC UA 프로토콜을 통해 데이터를 표준화했어. 이런 접근법 덕분에 전체 설비를 교체하지 않고도 통합된 디지털 트윈을 구축할 수 있었지! 🔧
이런 도전 과제들은 분명히 어렵지만, 적절한 전략과 접근법을 통해 극복할 수 있어. 중요한 것은 한 번에 모든 것을 완벽하게 하려고 하지 말고, 작게 시작해서 점진적으로 확장해 나가는 것이야. 디지털 트윈 여정은 마라톤이지 단거리 경주가 아니니까! 🏃♂️
또한, 이런 도전 과제를 해결하기 위해 다양한 전문가들의 협업이 필요해. 재능넷 같은 플랫폼을 통해 필요한 전문 인력을 찾고, 프로젝트 기반으로 협업하는 것도 좋은 방법이야. 특히 중소기업들에게는 모든 전문가를 정규직으로 고용하기보다 필요할 때 전문가의 재능을 활용하는 것이 비용 효율적일 수 있어! 💼
🔮 2025년 이후 디지털 트윈의 미래 트렌드
지금까지 2025년 현재의 디지털 트윈 기술과 구현 방법에 대해 알아봤어. 그렇다면 앞으로는 어떻게 발전할까? 2025년 이후 디지털 트윈 기술의 미래 트렌드를 살펴보자! 이런 트렌드를 미리 알아두면 장기적인 디지털 트윈 전략을 수립하는 데 도움이 될 거야. 🚀
1. 양자 컴퓨팅과 디지털 트윈의 결합 ⚛️
2026-2027년경에는 양자 컴퓨팅이 디지털 트윈에 적용되기 시작할 거야. 양자 컴퓨터는 기존 컴퓨터로는 불가능했던 복잡한 시뮬레이션을 수행할 수 있어. 예를 들어, 분자 수준의 재료 시뮬레이션이나 복잡한 유체 역학 계산을 실시간으로 처리할 수 있지.
이런 기술이 적용되면 제품 설계 단계에서 수천 가지 변수를 동시에 고려한 최적화가 가능해져. 예를 들어, 항공기 엔진의 모든 부품을 원자 수준에서 시뮬레이션하거나, 신약 개발 과정에서 분자 상호작용을 정확히 예측할 수 있게 될 거야. 이는 제품 개발 시간을 획기적으로 단축시키고, 혁신적인 설계를 가능하게 할 거야! 🚀
2. 메타버스와 디지털 트윈의 통합 🌐
2026년 이후에는 산업용 메타버스와 디지털 트윈이 통합되는 추세가 강해질 거야. 이는 단순한 3D 시각화를 넘어서, 몰입형 가상 환경에서 여러 전문가들이 함께 협업하며 디지털 트윈을 분석하고 조작할 수 있게 해줘.
예를 들어, 서울에 있는 엔지니어와 뉴욕에 있는 디자이너, 베를린에 있는 생산 관리자가 동시에 가상 공간에서 만나 디지털 트윈으로 구현된 공장을 함께 둘러보며 문제점을 논의하고 해결책을 테스트할 수 있어. 이런 협업 방식은 글로벌 팀의 효율성을 크게 높이고, 원격 작업의 한계를 극복하는 데 도움이 될 거야! 👨👩👧👦
3. 자율 디지털 트윈(Autonomous Digital Twins) 🤖
2028-2029년경에는 AI가 더욱 발전하면서 자율적으로 의사결정을 내리는 디지털 트윈이 등장할 거야. 이런 자율 디지털 트윈은 인간의 개입 없이도 스스로 학습하고, 최적화하고, 문제를 해결할 수 있어.
예를 들어, 공장의 자율 디지털 트윈은 날씨 변화, 원자재 가격 변동, 주문량 변화 등 다양한 외부 요인을 고려해 생산 계획을 자동으로 조정할 수 있어. 또한 예측 유지보수를 넘어, 기계 부품의 설계까지 자동으로 개선하는 수준에 도달할 거야. 이는 '자율 공장(Autonomous Factory)'이라는 개념으로 발전하게 될 거야! 🏭
4. 디지털 트윈 생태계(Digital Twin Ecosystems) 🌳
2030년 이후에는 개별 디지털 트윈들이 서로 연결되어 거대한 생태계를 형성하게 될 거야. 예를 들어, 공장의 디지털 트윈이 공급업체의 디지털 트윈, 물류 네트워크의 디지털 트윈, 심지어 고객 사용 환경의 디지털 트윈과도 연결될 수 있어.
이런 생태계에서는 전체 가치 사슬에 걸친 최적화가 가능해져. 예를 들어, 소비자 사용 패턴의 변화가 즉시 제조 공정에 반영되고, 이는 다시 공급망 전체에 영향을 미치는 식이야. 이를 통해 진정한 의미의 '수요 기반 생산(Demand-driven Manufacturing)'이 실현될 수 있어! 🔄
5. 6G 네트워크와 초연결 디지털 트윈 📡
2027-2028년경 상용화될 것으로 예상되는 6G 네트워크는 디지털 트윈에 혁명적인 변화를 가져올 거야. 테라비트급 전송 속도와 마이크로초 수준의 지연 시간은 실시간 초고해상도 디지털 트윈을 가능하게 해.
이런 네트워크 환경에서는 수백만 개의 센서에서 수집된 데이터를 실시간으로 처리하고, 홀로그래픽 디스플레이를 통해 초현실적인 시각화가 가능해질 거야. 또한 '인터넷 오브 센스(Internet of Senses)'라는 개념이 등장해, 디지털 트윈을 통해 원격으로 촉각, 후각까지 전달할 수 있게 될 거야! 🌐
6. 뉴로모픽 컴퓨팅과 초저전력 디지털 트윈 🧠
2029-2030년경에는 인간 뇌의 구조를 모방한 뉴로모픽 컴퓨팅 칩이 디지털 트윈에 적용될 거야. 이런 칩은 기존 프로세서보다 에너지 효율이 1000배 이상 높아, 초저전력으로 복잡한 AI 알고리즘을 실행할 수 있어.
이 기술이 적용되면 엣지 디바이스에서도 고급 디지털 트윈 기능을 구현할 수 있게 돼. 예를 들어, 작은 센서 노드에서도 복잡한 예측 분석을 수행할 수 있고, 배터리로 몇 년간 작동하는 자율 디지털 트윈 시스템을 구축할 수 있어. 이는 특히 원격 지역이나 극한 환경에서의 디지털 트윈 적용을 크게 확대할 거야! 🔋
7. 디지털 트윈과 합성 생물학의 융합 🧬
2030년 이후의 장기적 트렌드로, 디지털 트윈 기술이 합성 생물학과 융합되는 흐름이 예상돼. 생물학적 시스템(세포, 조직, 장기 등)의 디지털 트윈을 만들어 신약 개발, 질병 치료, 바이오 제조 등에 활용하는 거야.
예를 들어, 인간 장기의 디지털 트윈을 만들어 약물 반응을 시뮬레이션하거나, 미생물 공장의 디지털 트윈을 통해 바이오 연료나 의약품 생산 과정을 최적화할 수 있어. 이는 의료와 바이오 산업에 혁명적인 변화를 가져올 수 있는 분야야! 🔬
이런 미래 트렌드들은 지금 당장 구현하기는 어렵지만, 장기적인 디지털 트윈 전략을 수립할 때 고려해야 할 중요한 방향성이야. 특히 기술 발전 속도가 점점 빨라지고 있어서, 우리가 생각하는 것보다 이런 미래가 더 빨리 다가올 수도 있어! 🚀
물론 이런 첨단 기술을 모두 도입할 필요는 없어. 중요한 것은 자신의 비즈니스 목표와 필요에 맞는 기술을 선택하는 거야. 작게 시작해서 점진적으로 발전시켜 나가는 접근법이 여전히 가장 현실적이고 효과적인 전략이지! 🌱
🎯 마무리: 디지털 트윈 여정을 시작하자!
지금까지 디지털 트윈 기반 제조 시스템에 대해 정말 많은 내용을 알아봤어! 디지털 트윈이 무엇인지부터 시작해서, 핵심 구성요소, 구현 단계, 성공 사례, 도전 과제, 그리고 미래 트렌드까지... 정말 긴 여정이었지? 🚶♂️
이 모든 내용을 정리해보면, 디지털 트윈은 단순한 기술 트렌드가 아니라 제조업의 미래를 근본적으로 바꿀 혁신적인 패러다임이라는 것을 알 수 있어. 2025년 현재, 디지털 트윈은 이미 많은 기업들에게 생산성 향상, 비용 절감, 품질 개선, 혁신 가속화 등 다양한 혜택을 제공하고 있어.
하지만 디지털 트윈 여정은 결코 쉽지 않아. 데이터 통합, 보안, 인재 확보, ROI 증명 등 다양한 도전 과제가 있지. 그럼에도 불구하고, 적절한 전략과 단계적 접근법을 통해 이런 도전들을 극복하고 성공적인 디지털 트윈을 구현할 수 있어. 중요한 것은 비즈니스 목표를 명확히 하고, 작게 시작해서 점진적으로 확장해 나가는 것이야.
미래를 내다보면, 양자 컴퓨팅, 메타버스, 자율 시스템, 6G 네트워크 등의 기술 발전과 함께 디지털 트윈은 더욱 강력하고 지능적으로 진화할 거야. 이런 발전은 우리가 상상하지 못했던 새로운 가능성을 열어줄 거야!
🚀 디지털 트윈 여정을 시작하기 위한 첫 단계
- 비즈니스 목표 정의하기: 디지털 트윈을 통해 해결하고자 하는 구체적인 문제나 목표를 명확히 해.
- 현재 상태 평가하기: 데이터, 시스템, 인프라, 인재 등 현재 보유한 자원과 역량을 평가해.
- 파일럿 프로젝트 계획하기: 작은 규모로 시작할 수 있는 파일럿 프로젝트를 선정해.
- 전문가 네트워크 구축하기: 내부 팀 교육과 함께, 외부 전문가와의 협업 방안을 모색해.
- 지속적인 학습과 적응: 디지털 트윈 기술은 계속 발전하고 있으니, 지속적인 학습과 적응이 필요해.
재능넷에서는 디지털 트윈 구현에 필요한 다양한 전문가들을 만날 수 있어. 데이터 과학자, IoT 개발자, 3D 모델링 전문가, 클라우드 아키텍트 등 필요한 인재들과 프로젝트 기반으로 협업할 수 있는 좋은 기회가 될 거야! 🤝
마지막으로, 디지털 트윈은 기술적 도전이기도 하지만, 더 중요한 것은 조직 문화와 사고방식의 변화라는 점을 기억해. 데이터 기반 의사결정, 지속적인 혁신, 부서 간 협업 등 디지털 문화를 조성하는 것이 성공의 핵심이야.
이제 디지털 트윈의 세계로 첫 발을 내딛을 준비가 되었어? 미래 제조업의 핵심 기술을 통해 경쟁력을 높이고, 혁신을 가속화하는 여정을 시작해보자! 함께라면 더 멀리 갈 수 있을 거야! 🌟
🌟 디지털 트윈이 뭐길래 다들 난리야? 🌟
2025년 현재, 제조업계에서 가장 핫한 키워드를 꼽으라면 단연 '디지털 트윈'이지! 근데 이게 정확히 뭐냐고? 간단히 말하면 현실 세계의 물리적 대상을 디지털 공간에 쌍둥이처럼 똑같이 복제해놓은 거야. 마치 네가 게임 속에 아바타를 만들어 놓은 것처럼, 공장이나 기계, 제품 같은 것들을 컴퓨터 속에 가상으로 만들어 놓는 거지.
근데 그냥 3D 모델링이랑은 달라! 디지털 트윈은 실시간으로 현실 세계의 데이터를 받아서 똑같이 움직이고, 심지어 미래도 예측할 수 있어. 예를 들어, 실제 공장에 있는 로봇이 움직이면 디지털 트윈 속 가상 로봇도 똑같이 움직이는 거야. 더 놀라운 건 이 가상 로봇으로 여러 시나리오를 테스트해보고, 그 결과를 실제 로봇에 적용할 수 있다는 거지! 😲
재능넷에서 최근 디지털 트윈 관련 프로젝트들이 급증하고 있다는 사실, 알고 있었어? 많은 제조업체들이 디지털 트윈 시스템 구축을 위해 전문가들의 재능을 찾고 있거든. 특히 시뮬레이션 전문가, 데이터 분석가, IoT 개발자들의 수요가 엄청나게 늘고 있어! 🔥
이 글에서는 2025년 최신 트렌드를 반영한 디지털 트윈 기반 제조 시스템을 어떻게 구현하는지 쉽고 재미있게 알아볼 거야. 기술적인 내용도 있지만, 너무 어렵게 생각하지 마! 마치 레고 블록 쌓듯이 하나씩 알아가다 보면 어느새 디지털 트윈 전문가가 될 수 있을 거야. 함께 미래 제조업의 핵심 기술을 탐험해보자! 👊
🤔 왜 갑자기 디지털 트윈이 중요해진 거야?
2025년 현재, 제조업은 그 어느 때보다 빠르게 변화하고 있어. 코로나19 이후 글로벌 공급망 재편, 지속가능성에 대한 요구, 맞춤형 생산 수요 증가... 이런 변화에 적응하려면 더 민첩하고, 더 스마트하고, 더 효율적인 제조 시스템이 필요해졌지!
🌈 디지털 트윈이 가져다주는 혜택들
- 실시간 모니터링과 예측 유지보수 - 기계가 고장 나기 전에 미리 알 수 있어! 🔍
- 가상 시뮬레이션으로 위험 감소 - 실제로 해보기 전에 컴퓨터로 테스트해볼 수 있어서 안전해! 🛡️
- 생산 최적화 - 어떻게 배치하고 운영하는 게 가장 효율적인지 알 수 있어! ⚡
- 에너지 절약 - 불필요한 에너지 소비를 줄여서 친환경적이고 비용도 절감! 🌱
- 제품 개발 시간 단축 - 시장에 더 빨리 제품을 내놓을 수 있어! 🚀
재미있는 사실! 2025년 초 발표된 글로벌 제조업 리포트에 따르면, 디지털 트윈을 도입한 제조 기업들은 평균적으로 생산성이 25% 향상되고, 유지보수 비용이 30% 감소했다고 해. 이런 숫자들이 바로 기업들이 디지털 트윈에 투자하는 이유지! 💰
특히 2024년부터 시작된 글로벌 탄소중립 규제 강화로 인해, 많은 제조업체들이 에너지 효율성을 높이기 위한 방법으로 디지털 트윈을 선택하고 있어. 실제로 한 자동차 부품 제조업체는 디지털 트윈을 통해 공장 에너지 사용량을 22% 줄이면서도 생산량은 15% 늘렸다고 하니, 정말 대단하지 않아? 🌍
이런 효과들 때문에 2025년 현재 전 세계 제조업체의 약 45%가 이미 디지털 트윈을 도입했거나 도입 중이라고 해. 특히 자동차, 항공우주, 전자제품 제조 분야에서 가장 활발하게 적용되고 있지. 그리고 이 추세는 앞으로 더 가속화될 전망이야! 🚀
🧩 디지털 트윈 시스템의 핵심 구성요소
디지털 트윈이 뭔지는 알겠는데, 이걸 어떻게 만드는 거야? 🤔 걱정마! 복잡해 보이지만 핵심 구성요소들을 하나씩 살펴보면 이해하기 쉬워. 마치 레고 블록처럼 이 요소들을 조합하면 디지털 트윈 시스템이 완성되는 거지!
1. IoT 센서와 액추에이터 🔌
디지털 트윈의 눈과 귀라고 할 수 있어! 실제 물리적 환경에서 온도, 습도, 진동, 압력 등 다양한 데이터를 수집하는 센서들이지. 2025년에는 초소형 나노 센서와 자가발전 센서가 대세인데, 배터리 교체 없이도 몇 년간 작동할 수 있어서 정말 편리해졌어.
최신 트렌드로는 엣지 컴퓨팅 기능이 내장된 스마트 센서가 인기야. 이 센서들은 데이터를 중앙 서버로 보내기 전에 자체적으로 일부 처리를 할 수 있어서 네트워크 부하를 줄이고 실시간성을 높여줘! 🚀
2. 데이터 통합 플랫폼 💾
다양한 소스에서 수집된 데이터를 한곳에 모으고 정리하는 플랫폼이야. 이게 없으면 데이터가 서로 다른 형식으로 흩어져 있어서 활용하기 어려워. 2025년에는 클라우드 기반 데이터 레이크와 하이브리드 아키텍처가 표준이 되었어. 특히 AWS IoT SiteWise, Azure Digital Twins, Google Cloud IoT 같은 서비스들이 많이 사용되고 있지.
재능넷에서도 이런 데이터 통합 플랫폼 구축 전문가들의 재능이 인기 있다고 해! 특히 다양한 산업 프로토콜(OPC UA, MQTT, Modbus 등)을 통합할 수 있는 전문가들이 귀한 존재지. 🌟
3. 3D 모델링 및 시각화 🖼️
디지털 트윈의 얼굴이라고 할 수 있어! 실제 물리적 대상을 컴퓨터 안에 3D로 표현하는 기술이지. 단순한 3D 모델을 넘어서 물리 엔진을 적용해 실제 물리 법칙을 따르는 시뮬레이션이 가능해. 2025년에는 AR/VR과 결합된 몰입형 디지털 트윈이 대세야.
최신 트렌드로는 Unity, Unreal Engine 같은 게임 엔진을 산업용으로 활용하는 사례가 늘고 있어. 이런 툴들은 원래 게임을 만들기 위한 거였지만, 뛰어난 그래픽 성능과 물리 시뮬레이션 능력 때문에 디지털 트윈 구현에도 많이 사용되고 있어! 🎮
4. AI/ML 분석 엔진 🧠
디지털 트윈의 두뇌라고 할 수 있어! 수집된 데이터를 분석해서 패턴을 찾고, 이상 징후를 감지하고, 미래를 예측하는 역할을 해. 2025년에는 강화학습과 연합학습 기술이 제조업 AI에 많이 적용되고 있어.
특히 주목할 만한 트렌드는 '설명 가능한 AI(XAI)'야. 이전의 블랙박스 같은 AI와 달리, 왜 그런 결정을 내렸는지 이유를 설명할 수 있는 AI가 산업 현장에서 중요해졌어. 사람들이 AI의 판단을 신뢰하고 따르기 위해서는 그 이유를 이해할 수 있어야 하거든! 🤖
5. 클라우드/엣지 컴퓨팅 인프라 ☁️
디지털 트윈 시스템의 근육이라고 할 수 있어! 모든 데이터를 처리하고 저장하는 컴퓨팅 파워를 제공해. 2025년에는 클라우드와 엣지의 하이브리드 모델이 표준이 되었어. 중요한 실시간 처리는 현장의 엣지 서버에서, 대규모 데이터 분석과 저장은 클라우드에서 이루어지는 방식이지.
최신 트렌드로는 '서버리스 컴퓨팅'과 '컨테이너 오케스트레이션'이 있어. 특히 Kubernetes를 활용한 마이크로서비스 아키텍처가 디지털 트윈 시스템에 많이 적용되고 있어. 이렇게 하면 시스템의 각 부분을 독립적으로 업데이트하고 확장할 수 있거든! 📦
6. 사이버 보안 시스템 🔒
디지털 트윈의 방패라고 할 수 있어! 중요한 산업 데이터와 제어 시스템을 해커로부터 보호하는 역할을 해. 2025년에는 제로 트러스트 보안 모델과 AI 기반 위협 탐지가 필수가 되었어.
특히 OT(운영 기술)와 IT(정보 기술)의 융합으로 인해 사이버 보안의 중요성이 더욱 커졌어. 해커가 디지털 트윈을 통해 실제 공장 설비를 제어할 수도 있기 때문에, 강력한 보안 시스템이 필수적이지! 🛡️
이 모든 구성요소들이 유기적으로 연결되어 작동할 때 진정한 디지털 트윈이 완성돼! 마치 인체의 각 기관처럼, 각 요소가 자기 역할을 제대로 수행해야 전체 시스템이 원활하게 작동하는 거지. 다음 섹션에서는 이런 디지털 트윈 시스템을 실제로 어떻게 구현하는지 단계별로 알아볼게! 🚀
🛠️ 디지털 트윈 기반 제조 시스템 구현 단계
자, 이제 디지털 트윈이 뭔지, 어떤 구성요소로 이루어져 있는지 알았으니 실제로 어떻게 만드는지 알아볼 차례야! 2025년 최신 방법론을 기반으로 한 단계별 구현 가이드를 준비했어. 너무 어렵게 생각하지 말고, 하나씩 따라와 봐! 🚶♂️
1단계: 목표 설정 및 범위 정의 🎯
디지털 트윈을 만들기 전에 먼저 "왜 만드는지", "무엇을 디지털화할지" 명확히 해야 해. 모든 것을 한번에 디지털 트윈으로 만들려고 하면 실패하기 쉬워. 작은 범위에서 시작해서 점진적으로 확장하는 게 2025년 현재 가장 성공률이 높은 접근법이야.
✅ 체크리스트:
- 어떤 비즈니스 문제를 해결하려는가? (예: 생산성 향상, 품질 개선, 에너지 절약)
- 어떤 자산이나 프로세스를 디지털화할 것인가? (예: 특정 생산라인, 개별 기계, 전체 공장)
- 어떤 데이터가 필요한가? (예: 온도, 압력, 진동, 에너지 사용량)
- ROI(투자수익률)는 어떻게 측정할 것인가?
- 주요 이해관계자는 누구인가? (경영진, 운영자, 유지보수팀 등)
2025년 트렌드: 최근에는 '밸류 스트림 매핑'이라는 방법을 많이 사용해. 전체 가치 흐름에서 가장 개선이 필요한 부분을 찾아내고, 그곳에 디지털 트윈을 우선 적용하는 거지. 이렇게 하면 투자 대비 효과를 빨리 볼 수 있어! 💸
2단계: 데이터 전략 수립 및 센서 인프라 구축 📊
디지털 트윈의 품질은 데이터의 품질에 직결돼. 어떤 데이터가 필요한지, 어떻게 수집할지, 얼마나 자주 수집할지 등을 결정해야 해. 그리고 필요한 센서와 데이터 수집 인프라를 구축하는 단계야.
🔍 주요 고려사항:
- 필요한 센서 유형 및 수량 (온도, 압력, 진동, 전력, 위치 등)
- 센서 정확도 및 샘플링 빈도 (초당 몇 번 데이터를 수집할지)
- 유선 vs. 무선 센서 네트워크 (2025년에는 5G/6G 기반 무선 센서가 대세)
- 데이터 전처리 전략 (엣지에서 얼마나 처리할지, 클라우드로 얼마나 보낼지)
- 기존 시스템(MES, ERP, SCADA 등)과의 통합 방안
실제 코드 예시: 2025년에는 Python과 Node-RED를 활용한 센서 데이터 수집이 일반적이야. 간단한 MQTT 기반 센서 데이터 수집 코드를 살펴볼까?
# Python으로 MQTT 센서 데이터 수집하기
import paho.mqtt.client as mqtt
import json
import time
from datetime import datetime
# MQTT 브로커 설정
broker_address = "mqtt.factory.local"
port = 1883
topic = "sensors/production_line_1/#"
# 콜백 함수 정의
def on_message(client, userdata, message):
try:
# 데이터 파싱
payload = json.loads(message.payload.decode("utf-8"))
sensor_id = payload["sensor_id"]
value = payload["value"]
timestamp = payload["timestamp"]
# 타임스탬프 변환
dt = datetime.fromtimestamp(timestamp)
formatted_time = dt.strftime("%Y-%m-%d %H:%M:%S")
# 데이터 처리 및 저장
print(f"센서 {sensor_id}에서 {formatted_time}에 {value} 값을 수신했습니다.")
# 여기에 데이터베이스 저장 로직 추가
except Exception as e:
print(f"데이터 처리 중 오류 발생: {e}")
# MQTT 클라이언트 설정
client = mqtt.Client("DigitalTwinDataCollector")
client.on_message = on_message
# 브로커 연결
client.connect(broker_address, port)
client.subscribe(topic)
# 메시지 수신 루프 시작
print("센서 데이터 수신 대기 중...")
client.loop_forever()
2025년 트렌드: 최근에는 '디지털 스레드(Digital Thread)'라는 개념이 중요해졌어. 이는 제품 수명 주기 전체에 걸쳐 데이터의 연속성을 유지하는 것을 의미해. 설계부터 생산, 운영, 유지보수까지 모든 데이터가 끊김 없이 연결되어야 진정한 디지털 트윈이 완성된다는 개념이지! 🧵
3단계: 3D 모델링 및 시각화 환경 구축 🖥️
이제 실제 물리적 대상을 디지털 공간에 표현할 차례야. CAD 모델을 기반으로 3D 디지털 트윈을 만들고, 실시간 데이터와 연동시키는 단계지. 2025년에는 게임 엔진 기반 시각화가 대세야!
🛠️ 주요 도구 및 기술:
- 3D 모델링 도구: AutoCAD, SolidWorks, Blender, Revit
- 게임 엔진: Unity Industrial, Unreal Engine 6.0, NVIDIA Omniverse
- 시각화 프레임워크: Three.js, Babylon.js, WebGL
- AR/VR 통합: Microsoft HoloLens 3, Meta Quest Pro 2, Apple Vision Pro
- 클라우드 렌더링: AWS Nimble Studio, Google Cloud Rendering
2025년 트렌드: 최근에는 '포토리얼리스틱 디지털 트윈'이 인기야. 단순한 3D 모델이 아니라 실제와 거의 구분이 안 될 정도로 사실적인 렌더링을 제공하는 거지. 특히 NVIDIA의 RTX 기술을 활용한 실시간 레이 트레이싱이 산업용 디지털 트윈에도 적용되고 있어! 🎨
4단계: 데이터 통합 및 분석 플랫폼 구축 🔄
이제 센서에서 수집한 데이터와 3D 모델을 연결하고, 분석 기능을 추가할 차례야. 실시간 데이터 처리, 저장, 분석을 위한 백엔드 시스템을 구축하는 단계지.
🧩 주요 구성요소:
- 데이터 통합 미들웨어: Apache Kafka, RabbitMQ, MQTT 브로커
- 시계열 데이터베이스: InfluxDB, TimescaleDB, Amazon Timestream
- 분석 엔진: Apache Spark, TensorFlow, PyTorch
- API 게이트웨이: Kong, AWS API Gateway, Azure API Management
- 대시보드 도구: Grafana, Power BI, Tableau
실제 코드 예시: 2025년에는 시계열 데이터베이스와 AI 모델을 연동하는 것이 일반적이야. 간단한 예측 유지보수 모델 코드를 살펴볼까?
# Python으로 예측 유지보수 모델 구현하기
import pandas as pd
import numpy as np
from sklearn.ensemble import IsolationForest
from influxdb_client import InfluxDBClient
# InfluxDB 연결 설정
url = "http://influxdb.factory.local:8086"
token = "your_influxdb_token"
org = "your_organization"
bucket = "machine_data"
# 데이터 가져오기
client = InfluxDBClient(url=url, token=token, org=org)
query_api = client.query_api()
query = f'''
from(bucket: "{bucket}")
|> range(start: -7d)
|> filter(fn: (r) => r["_measurement"] == "vibration_data")
|> filter(fn: (r) => r["machine_id"] == "pump_101")
|> aggregateWindow(every: 1h, fn: mean)
'''
result = query_api.query_data_frame(query)
# 이상 탐지 모델 학습
model = IsolationForest(contamination=0.05, random_state=42)
model.fit(result[['_value']])
# 새로운 데이터에 대한 이상 탐지
def detect_anomalies(new_data):
# 데이터 전처리
new_data = new_data.reshape(-1, 1)
# 이상 점수 계산 (-1에 가까울수록 이상치)
anomaly_scores = model.decision_function(new_data)
anomaly_labels = model.predict(new_data)
# 결과 반환
return {
"scores": anomaly_scores,
"is_anomaly": [1 if label == -1 else 0 for label in anomaly_labels]
}
# 실시간 모니터링 함수
def monitor_machine_health():
print("기계 상태 모니터링 중...")
# 여기에 실시간 데이터 스트리밍 및 분석 로직 추가
# 알림 설정
def send_alert(machine_id, anomaly_score):
print(f"⚠️ 경고: 기계 {machine_id}에서 이상 징후 감지! 점수: {anomaly_score:.2f}")
# 여기에 SMS, 이메일, 모바일 앱 알림 등의 코드 추가
2025년 트렌드: 최근에는 '디지털 트윈 오케스트레이션'이라는 개념이 등장했어. 여러 개의 디지털 트윈을 연결해서 전체 시스템을 통합적으로 관리하는 거지. 예를 들어, 개별 기계의 디지털 트윈들이 모여서 생산라인의 디지털 트윈을 구성하고, 여러 생산라인의 디지털 트윈이 모여서 공장 전체의 디지털 트윈을 구성하는 식이야! 🎼
5단계: 시뮬레이션 및 최적화 기능 개발 🔬
이제 디지털 트윈의 가장 강력한 기능인 시뮬레이션과 최적화 기능을 추가할 차례야. '만약 이렇게 하면 어떻게 될까?'라는 질문에 답할 수 있는 기능을 개발하는 단계지.
🚀 주요 시뮬레이션 유형:
- 이산 사건 시뮬레이션: 생산 라인의 병목 현상 분석
- 물리 기반 시뮬레이션: 기계 부품의 마모 및 고장 예측
- 몬테카를로 시뮬레이션: 다양한 변수에 따른 생산량 예측
- 디지털 쉐도잉: 실제 시스템과 디지털 트윈 간의 차이 분석
- 강화학습 기반 최적화: 최적의 생산 파라미터 도출
2025년 트렌드: 최근에는 '하이퍼 오토메이션'이라는 개념이 주목받고 있어. 디지털 트윈이 AI와 결합해서 자동으로 최적의 운영 조건을 찾고, 필요한 경우 실제 시스템에 적용까지 하는 거지. 사람의 개입 없이도 시스템이 스스로 최적화되는 단계로 발전하고 있어! 🤖
6단계: 사용자 인터페이스 및 대시보드 개발 👨💻
이제 사용자들이 디지털 트윈과 상호작용할 수 있는 인터페이스를 만들 차례야. 직관적이고 사용하기 쉬운 UI/UX를 개발하는 단계지. 2025년에는 AR/VR 기반 인터페이스가 대세야!
📱 주요 UI/UX 요소:
- 실시간 대시보드: KPI, 알림, 상태 모니터링
- 3D 인터랙티브 뷰: 확대/축소, 회전, 단면 보기
- AR 오버레이: 실제 기계 위에 데이터 표시
- VR 몰입 환경: 가상 공간에서의 협업 및 교육
- 음성 명령 인터페이스: 핸즈프리 조작
2025년 트렌드: 최근에는 '멀티모달 인터페이스'가 주목받고 있어. 터치, 음성, 제스처, 시선 추적 등 다양한 방식으로 디지털 트윈과 상호작용할 수 있는 거지. 특히 공장 현장에서는 양손이 자유롭지 않은 경우가 많아서, 음성 명령이나 AR 글래스를 통한 인터페이스가 인기를 끌고 있어! 👓
7단계: 테스트, 검증 및 배포 🧪
모든 시스템이 준비되었다면, 이제 테스트하고 검증한 후 실제 환경에 배포할 차례야. 디지털 트윈이 실제 물리적 대상과 정확히 일치하는지 확인하는 중요한 단계지.
✅ 검증 방법론:
- 디지털 쉐도잉: 실제 시스템과 디지털 트윈을 나란히 실행하며 비교
- 히스토리컬 데이터 테스트: 과거 데이터로 디지털 트윈의 정확도 검증
- A/B 테스팅: 디지털 트윈의 최적화 제안을 일부 영역에만 적용하여 효과 검증
- 스트레스 테스트: 극한 상황에서의 디지털 트윈 성능 검증
- 사용자 수용성 테스트: 실제 사용자들의 피드백 수집
2025년 트렌드: 최근에는 '지속적 검증(Continuous Validation)'이라는 개념이 중요해졌어. 한 번 검증하고 끝나는 게 아니라, 실제 시스템과 디지털 트윈 간의 차이를 지속적으로 모니터링하고 보정하는 거지. 이를 통해 시간이 지나도 디지털 트윈의 정확도를 유지할 수 있어! 🔄
8단계: 운영 및 지속적 개선 🔄
디지털 트윈은 한 번 만들고 끝나는 게 아니야. 지속적으로 데이터를 수집하고, 모델을 개선하고, 새로운 기능을 추가해야 해. 이것이 디지털 트윈의 진정한 가치를 실현하는 방법이지!
🔄 지속적 개선 전략:
- 모델 드리프트 모니터링: 디지털 트윈과 실제 시스템 간의 차이 추적
- 자동 모델 재학습: 새로운 데이터로 AI 모델 주기적 업데이트
- 피드백 루프 구축: 사용자 피드백을 시스템 개선에 반영
- 새로운 센서 및 데이터 소스 통합: 데이터 수집 범위 확장
- 디지털 트윈 확장: 더 많은 자산과 프로세스로 범위 확대
2025년 트렌드: 최근에는 '자기 진화형 디지털 트윈(Self-evolving Digital Twin)'이라는 개념이 등장했어. AI가 스스로 학습하면서 디지털 트윈 모델을 자동으로 개선하는 거지. 사람의 개입 없이도 시간이 지날수록 더 정확하고 유용해지는 디지털 트윈을 만드는 것이 목표야! 🌱
이렇게 8단계를 거치면 디지털 트윈 기반 제조 시스템이 완성돼! 물론 각 단계마다 세부적인 작업들이 많지만, 큰 그림으로는 이런 흐름을 따른다고 보면 돼. 다음 섹션에서는 실제 산업 현장에서 디지털 트윈이 어떻게 활용되고 있는지 사례를 통해 알아볼게! 🏭
📚 2025년 최신 디지털 트윈 성공 사례
이론은 충분히 알아봤으니, 이제 실제로 기업들이 디지털 트윈을 어떻게 활용하고 있는지 살펴볼까? 2025년 현재 가장 주목받는 디지털 트윈 성공 사례들을 소개할게! 이 사례들을 통해 디지털 트윈의 실질적인 가치와 적용 방법을 더 구체적으로 이해할 수 있을 거야. 🔍
🚗 테슬라의 기가팩토리 디지털 트윈
도전 과제: 테슬라는 2024년 출시한 새로운 배터리 생산 라인의 효율성을 극대화하고, 에너지 사용량을 줄이며, 불량률을 최소화해야 했어.
솔루션: 테슬라는 네바다 기가팩토리의 완벽한 디지털 트윈을 구축했어. 수천 개의 IoT 센서, 컴퓨터 비전 카메라, 로봇 데이터를 통합하고, NVIDIA Omniverse 플랫폼을 활용해 포토리얼리스틱 3D 모델을 만들었지. 특히 주목할 만한 점은 강화학습 기반 최적화 알고리즘을 적용해 생산 파라미터를 자동으로 조정한다는 거야.
결과: 디지털 트윈 도입 후 1년 만에 테슬라는 배터리 생산량을 32% 증가시켰고, 에너지 소비는 18% 감소시켰어. 또한 불량률이 45% 감소했고, 신제품 출시 시간이 30% 단축되었지. 테슬라의 CFO는 "디지털 트윈 프로젝트는 1년 만에 투자 비용을 회수했다"고 밝혔어.
핵심 기술: NVIDIA Omniverse, Azure Digital Twins, PyTorch 기반 강화학습, 5G 프라이빗 네트워크
🏭 지멘스의 스마트 팩토리 디지털 트윈
도전 과제: 지멘스는 독일 암베르크 공장에서 1,000개 이상의 제품 변형을 유연하게 생산하면서도 높은 품질과 효율성을 유지해야 했어.
솔루션: 지멘스는 자사의 MindSphere 플랫폼을 기반으로 전체 공장의 엔드투엔드 디지털 트윈을 구축했어. 이 디지털 트윈은 제품 설계, 생산 계획, 공정 시뮬레이션, 실시간 모니터링을 모두 통합했지. 특히 '디지털 스레드' 개념을 적용해 제품 수명 주기 전체에 걸쳐 데이터의 연속성을 유지했어.
결과: 디지털 트윈 덕분에 지멘스는 생산 라인 전환 시간을 60% 단축했고, 에너지 효율성은 25% 향상되었어. 또한 품질 문제를 실시간으로 감지하고 해결함으로써 불량률을 80% 감소시켰지. 가장 인상적인 것은 99.9996%의 품질 정확도를 달성했다는 점이야!
핵심 기술: Siemens MindSphere, Tecnomatix, NX CAD, TIA Portal, 에지 컴퓨팅
✈️ 에어버스의 항공기 디지털 트윈
도전 과제: 에어버스는 새로운 수소 추진 항공기 개발 과정에서 설계 최적화, 테스트 비용 절감, 인증 프로세스 가속화가 필요했어.
솔루션: 에어버스는 항공기의 전체 수명 주기를 아우르는 디지털 트윈을 개발했어. 설계 단계부터 운영, 유지보수까지 모든 데이터를 통합한 거지. 특히 CFD(전산유체역학) 시뮬레이션과 구조 분석을 실시간으로 수행할 수 있는 고성능 컴퓨팅 인프라를 구축했어.
결과: 디지털 트윈 덕분에 에어버스는 물리적 프로토타입 수를 75% 줄였고, 개발 시간을 2년 단축했어. 또한 시뮬레이션을 통해 발견된 설계 최적화로 연료 효율성이 15% 향상되었지. 가장 중요한 것은 안전 인증 과정이 크게 가속화되어 시장 출시 시간이 단축되었다는 점이야.
핵심 기술: Dassault Systèmes 3DEXPERIENCE, HPC 클라우드 컴퓨팅, 디지털 인증 프레임워크
🤖 삼성전자의 반도체 공장 디지털 트윈
도전 과제: 삼성전자는 최첨단 3나노 반도체 생산 과정에서 수율 향상, 에너지 효율화, 생산 일정 최적화가 필요했어.
솔루션: 삼성은 평택 반도체 공장의 멀티스케일 디지털 트윈을 구축했어. 개별 장비부터 전체 공정 라인, 그리고 공장 전체까지 다양한 스케일의 디지털 트윈을 계층적으로 연결한 거지. 특히 주목할 만한 점은 양자 컴퓨팅 알고리즘을 활용한 공정 최적화 시스템을 도입했다는 거야.
결과: 디지털 트윈 덕분에 삼성은 신규 공정의 수율을 초기부터 85%로 높일 수 있었고, 이는 기존 방식보다 30% 향상된 수치야. 또한 에너지 사용량이 22% 감소했고, 장비 가동률이 17% 증가했지. 가장 인상적인 것은 예측 유지보수 시스템을 통해 계획되지 않은 다운타임을 93% 감소시켰다는 점이야!
핵심 기술: 삼성 자체 개발 SDTP(Samsung Digital Twin Platform), AWS 양자 컴퓨팅, 6G 프라이빗 네트워크
이런 성공 사례들을 보면 디지털 트윈이 단순한 기술 트렌드가 아니라, 제조업의 미래를 근본적으로 바꾸는 혁신적인 접근법이라는 것을 알 수 있어. 각 기업들은 자신들의 특정 문제를 해결하기 위해 디지털 트윈을 맞춤형으로 구현했고, 그 결과 생산성, 품질, 효율성 측면에서 놀라운 성과를 거두었지! 🚀
재능넷에서도 이런 디지털 트윈 구현 프로젝트에 참여할 수 있는 다양한 전문가들을 만날 수 있어. 데이터 과학자, 3D 모델링 전문가, IoT 개발자, 클라우드 아키텍트 등 디지털 트윈 구현에 필요한 모든 인재들이 재능넷 플랫폼을 통해 협업하고 있지! 🤝
- 지식인의 숲 - 지적 재산권 보호 고지
지적 재산권 보호 고지
- 저작권 및 소유권: 본 컨텐츠는 재능넷의 독점 AI 기술로 생성되었으며, 대한민국 저작권법 및 국제 저작권 협약에 의해 보호됩니다.
- AI 생성 컨텐츠의 법적 지위: 본 AI 생성 컨텐츠는 재능넷의 지적 창작물로 인정되며, 관련 법규에 따라 저작권 보호를 받습니다.
- 사용 제한: 재능넷의 명시적 서면 동의 없이 본 컨텐츠를 복제, 수정, 배포, 또는 상업적으로 활용하는 행위는 엄격히 금지됩니다.
- 데이터 수집 금지: 본 컨텐츠에 대한 무단 스크래핑, 크롤링, 및 자동화된 데이터 수집은 법적 제재의 대상이 됩니다.
- AI 학습 제한: 재능넷의 AI 생성 컨텐츠를 타 AI 모델 학습에 무단 사용하는 행위는 금지되며, 이는 지적 재산권 침해로 간주됩니다.
재능넷은 최신 AI 기술과 법률에 기반하여 자사의 지적 재산권을 적극적으로 보호하며,
무단 사용 및 침해 행위에 대해 법적 대응을 할 권리를 보유합니다.
© 2025 재능넷 | All rights reserved.
댓글 0개